Wholesale price for ASTM A194 4 Heavy Hex Nuts for Congo Factories
Short Description:
ASTM A194/A194M 4 Heavy Hex Nuts API 6A Flange Valve Wellhead Heavy Hex Nuts Dimension Standard: ASME B18.2.2, ASME B18.2.4.6M, ISO 4033, Din934 H=D Inch Size: 1/4”-4” with various lengths Metric Size: M6-M100 with various lengths Other Available Grade: ASTM A194/A194M 2H, 2HM, 4, 4L, 7, 7L, 7M, 8, 8M, 16 and so on. Finish: Plain, Black Oxide, Zinc Plated, Zinc Nickel Plated, Cadmium Plated, PTFE etc. Packing: Bulk about 25 kgs each carton, 36 cartons each pallet Advantage: High Quality, Comp...
Product Detail
Product Tags
Wholesale price for ASTM A194 4 Heavy Hex Nuts for Congo Factories Detail:
ASTM A194/A194M 4 Heavy Hex Nuts
API 6A Flange Valve Wellhead Heavy Hex Nuts
Dimension Standard: ASME B18.2.2, ASME B18.2.4.6M, ISO 4033, Din934 H=D
Inch Size: 1/4”-4” with various lengths
Metric Size: M6-M100 with various lengths
Other Available Grade:
ASTM A194/A194M 2H, 2HM, 4, 4L, 7, 7L, 7M, 8, 8M, 16 and so on.
Finish: Plain, Black Oxide, Zinc Plated, Zinc Nickel Plated, Cadmium Plated, PTFE etc.
Packing: Bulk about 25 kgs each carton, 36 cartons each pallet
Advantage: High Quality, Competitive Price, Timely Delivery,Technical Support, Supply Test Reports
Please feel free to contact us for more details.
Product detail pictures:
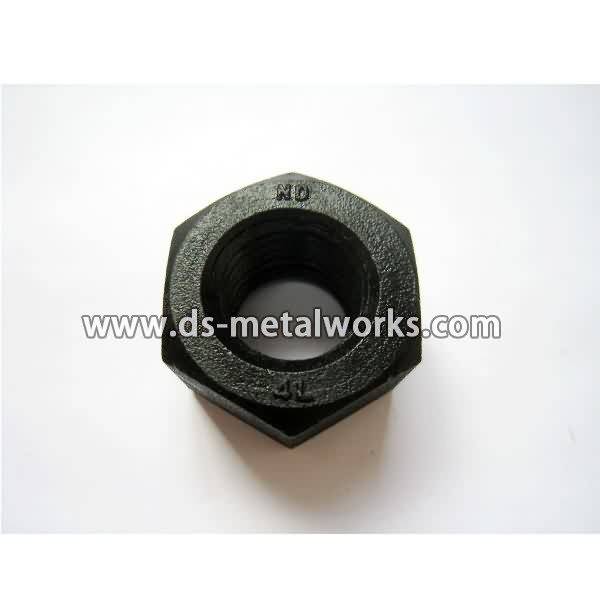
The key to our success is Good Product Excellent, Reasonable Rate and Efficient Service for Wholesale price for ASTM A194 4 Heavy Hex Nuts for Congo Factories, The product will supply to all over the world, such as: Lyon, Ecuador, Azerbaijan, Our products are widely recognized and trusted by users and can meet continuously developing economic and social needs. We welcome new and old customers from all walks of life to contact us for future business relationships and achieving mutual success!
Chongolian stickers, cards & prints: https://www.redbubble.com/people/chongolio/shop
Instagram: https://www.instagram.com/chongolio1
Make a do it yourself recycled soda can whirligig wind spinner using an aluminum can, tea can, pop can, or beer can.
https://www.chongolio.com/recycled-aluminum-can-wind-spinners-vlog23.
If you like kinetic art, this aluminum can art project is awesome and this video will show you how to make a beer can wind spinner or how to make soda can wind spinners.
Watch VLOG 23 for wind spinner instructions on how to build this found art object project.
Wind powered art is perfect for colorful garden art and garden decoration and is an easy to make recycled art project.
If you have a moment I sure would like to hear what you think of this beer can whirligig so please leave me a comment.
For this art project you will need:
An aluminum or pop can (Arizona ice tea cans are my favorite to use)
Scissors
Pliers (flower printed one are optional)
Gloves (highly recommended!)
A wire hanger
A wine cork
Furniture glides or a long skinny nail with a wide flat head
Screw and washer to secure base to wood fence or stake (optional)
The scissors are going to used to cut the top of the can and also to make and help shape the spinners blades. We are going to use this cork to secure the win spinner to its base. Pliers will be used to bend the coat hanger base. Please make a note here I do not own flowery pliers, these belong to my mom.
This pack of furniture glides will come in handy to attach the can to the cork. And lastly a coat hanger which is gonna serve as our base. The first step is to cut the top of the can. Use the scissors to carefully punch a hole the end. Once you have a hole, use that as a starting point to cut around the can.
You should really be wearing a pair gloves, because the edge of the can are pretty sharp, but since all I could find a flowery gloves I decided to just take my chances. Now lets make some blades by cutting slats vertically up the side of the can. Use any straight lines that you can find to act as guides.
Turning the scissors side ways and at an angle will help make longer cuts when you reach the other side of the can. Stop your cuts about half an inch from the bottom. Make another cut opposite the first one and then two more at 90 degree angles from the first two cuts.
Divide and cut those four blades in half to give you total 8 blades. As you cut those remaining blades, bend them outward horizontally.This will make them easier to cut those final slats.
Round the corners of the blades with your scissors on one side then flip the can over to easily do the same to the other side the blades. One last wee snip is made at the base of the blades which allows you to give it a slight bend so that he can catch the wind.
So now let’s get the base ready. With your pliers unwind the hook of the hangar and do your best to get the coat hanger as straight as possible. Make a right angle at the end of the hanger where the wire still has the twist in it from where it was wrapped around itself.
You can use the pliers to bend and break the curved part of the hanger just before the twists. On opposite side of the hanger, make another right angle. Depending on how tall you want your wind spinner to stand, you are gonna want to leave one to two feet between bends.
After you make that right angle, measure out three to four inches the go ahead and bend and break the hanger again. Fashion loop on that just bent side of the hanger so that you can use the washer and a screw to attach the base to something solid.
The pointy end of the furniture glides or a small nail can be used to put a hole in the end your cork. Now you can screw the cork onto the twisty end of the coat hanger. Poke a hole in the center of the can then use a discarded piece of the coat hanger to widen the hole just a little bit.
Using the furniture glide make a guide hole in the other in the cork, You will then be ready to attach the spinner to its base. Make sure you leave enough play for the can spin freely, then go ahead and fix any blades that may have gotten bent when you were putting the can on the cork.
Now go outside and find a nice breezy place to put your new wind spinner and let that thing do some spin in the wind So there, you go a wind spinner made easy peasy George and Weezy. Jefferson that is. Another simple project that you can make using items and tools that you probably have laying around your house.
Hey, if you got a project out there that you like to see me make why don’t leave me a comment down below. Send me an email or come find me on Facebook, Twitter or Google plus. You can also check my website out at Chonglio.com, Where I got all kinds of tips tricks and techniques to help release your inner artist.
How To Make A Clock In The Home Machine Shop – Part 4, by Clickspring.
In this video I go through the setup for cutting clock wheels, and cut the teeth for the 3rd wheel of the John Wilding “Large Wheel Skeleton Clock” project..
This is basically a light milling operation, carried out on the lathe, using a cross-slide mounted vertical slide, a light duty milling spindle, and a Sherline motor/speed control.
I also introduce the latest acquisition for the shop – a Divisionmaster cnc indexer.
Be sure to use breathing protection whenever you are heating super glue.
Thanks for watching. If you enjoyed the video please give a thumbs up, and a comment.
If you would like to help support the creation of these videos, then head on over to the Clickspring Patreon page: https://www.patreon.com/clickspring
For more info on this build, as well as other tool making info, visit the blog site at https://www.clickspringprojects.com
Other Videos to Watch:
How To Make A Clock Part 3 – Making The Washers and Screws
https://youtu.be/KXzyCM23WPI
How To Machine A Small Lathe Carrier
https://youtu.be/zB9XhqzBNJs
Ask Me A Question:
https://www.clickspringprojects.com/contact.html
Follow Clickspring:
https://www.facebook.com/Clickspring1
https://plus.google.com/u/0/113668471124073837794/posts
https://instagram.com/clickspring1/
https://www.tumblr.com/blog/clickspring1
https://twitter.com/clickspring1
https://www.patreon.com/clickspring
Transcript:
00:24 As to why clockmakers call gears “wheels”, I haven’t really found a good answer, but if it has 20 or more teeth its called a wheel, and if it has less than 20, its called a pinion.
00:46 So lets get into it. Starting out with a sheet of 1/16″ engravers brass, I lightly marked the center, and then roughed out a blank. You’re going to see me use these super glue arbors a lot as I make this clock. They’re perfect for holding workpieces that need to be machined on the edges.
01:12 The face of the chuck can be trued up if needed, little glue is applied, and then the rough blank is held in place with the tailstock for a few minutes while it sets. Its sort of a modern version of the shellac wax chuck that watchmakers have traditionally used. I turned the blank to the correct outside diameter, and then drilled and bored the center hole.
02:16 I made an adaptor plate for a myford vertical slide to fit the cross-slide, and also a platform that’ll hold the motor and speed control. A spindle is mounted on the vertical slide, and then indicated to be square.
02:40 The cutter is mounted on an arbor, and locked into the spindle, and then its lined up on the center of the work. In this case I’m using a centering button to identify the wheel center. The belt is tensioned to be tight at the full depth of cut, and thats the cutting setup all ready to go.
03:11 For dividing, I have these classic dividing plates, but the 290 tooth “Great Wheel” is a problem.
03:28 I had to make a few bits and pieces to make it work for my setup, like this expanding mandrel for the rear of the lathe, as well as support brackets. But this stuff only needs to be made once, and then its good to go for the future. So this is how the dividing mechanism fits onto my lathe.
04:15 The first step is to establish the correct depth of cut, and to do this, I took repeated cuts on either side of a single tooth, slightly lowering the cutter after each pass.
04:59 At that point, the cutter is at the correct depth to form the teeth, the vertical slide is locked, and then all of the teeth are cut in one pass. After all of the setup, the actual cutting of the teeth is pretty straight forward. The wheel can be taken off with a bit of heat.
06:21 Here’s the arbor for the stop work wheels. These teeth are a little long, so I made this one thicker, and just machined it away along with the brass to keep the teeth well supported during the cutting; same goes for the escape wheel.
06:33 The center wheel arbor is fabricated from 2 parts, as is the arbor for the great wheel. Apart from size, its essentially same thing in each case. Some wheels require different profile cutters. The escape wheel for instance, and the ratchet.
07:03 large tooth pitch, so it required a custom cutter. I used this button tool to form the tooth profile, It also needed its own custom arbor to mount it into the spindle.
07:15 and here’s the finished cutter, hardened and tempered. Other than those differences, its all pretty much the same for each wheel.
References:
John Wilding workshop and clock construction books:
https://www.ritetimepublishing.com/
Bill Smith, Master Clockmaker:
(Super Glue Arbor)
https://www.wrsmithtelegraphkeys.com
Lester Caine – Divisionmaster
https://medw.co.uk/wiki/DivisionMaster
How To Make A Clock In The Home Machine Shop – Part 4, by Clickspring.